Since When Have We Used Ebony for the Fingerboard?
When it comes to lutherie, the ebony fingerboard stands out as one of the most iconic components. Since its earliest use, this wood has been essential not only for its mechanical properties but also for its elegance. In this article, I want to share what makes ebony so unique—both from my experience as a luthier and from my work with the Maderas Barber team, where I have the opportunity to work with one of the largest selections of this wood on the market.
Ebony’s Introduction to the Lutherie Workshop
The use of ebony in lutherie dates back to the 16th century, when major European instrument-making workshops began experimenting with exotic woods brought by traders from Asia and Africa. Among these woods, ebony stood out for its uniform black color and exceptional hardness.
While early medieval string instruments primarily used local woods like maple and spruce, ebony was quickly adopted for components such as fingerboards, pegs, and tailpieces. Its resistance to wear and smooth texture made it the ideal material for parts of the instrument that are in constant contact with the musician’s hands.
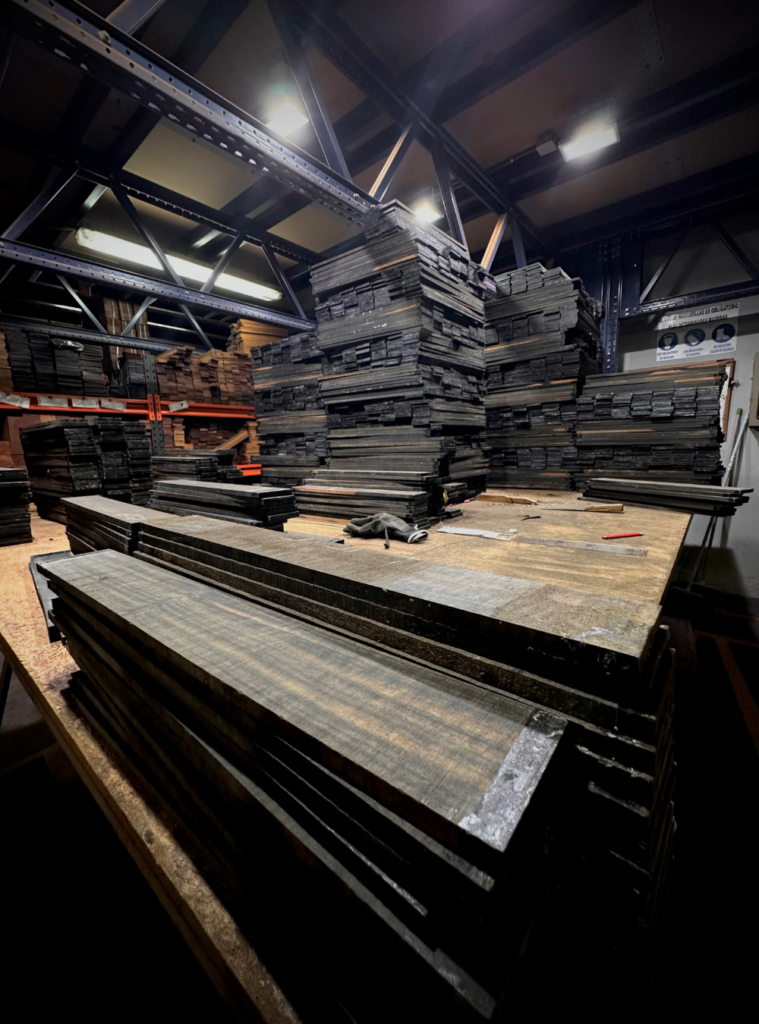
Ebony in Modern Lutherie
Ebony is a wood that challenges both the luthier and the workshop tools. Its extreme density and compact texture allow for flawless finishes, making it ideal for fingerboards, pegs, and tailpieces. However, these same characteristics demand precision in craftsmanship—the cuts must be clean, and the polishing meticulous to highlight both its uniform surface and resistance to wear.
Ebony trees are not homogeneous; each trunk produces pieces with unique characteristics and varying qualities. At Maderas Barber, as producers, they offer ebony of different grades, reflecting a commitment to making the most of this valuable raw material. This taught me that the goal isn’t to seek perfect uniformity, but rather to understand the distinct qualities of each piece and how to use them effectively in the instrument. In the end, it is the luthier who defines the character of ebony through their craftsmanship.

Ebony: A Super Wood for Luthiers
Ebony is not just a wood; it is an essential element in the tradition of lutherie, a material that connects centuries of history with the hands of today’s luthiers. Each piece, with its nuances and challenges, presents an opportunity to create something unique.
For me, working with ebony is a constant lesson in humility and learning, a reminder that wood has as much character as the instrument it becomes a part of.
Did you know this story about ebony?
What other aspects of tonewoods in lutherie would you like to explore?
Leave your comment on the blog, and let’s keep the conversation going!
Violins and Violas for Sale
Since When Have We Used Ebony for the Fingerboard?
When it comes to lutherie, the ebony fingerboard stands out as one of the most iconic components. Since its earliest use, this wood has been essential not only for its mechanical properties but also for its elegance. In this article, I want to share what makes ebony so unique—both from my experience as a luthier and from my work with the Maderas Barber team, where I have the opportunity to work with one of the largest selections of this wood on the market.
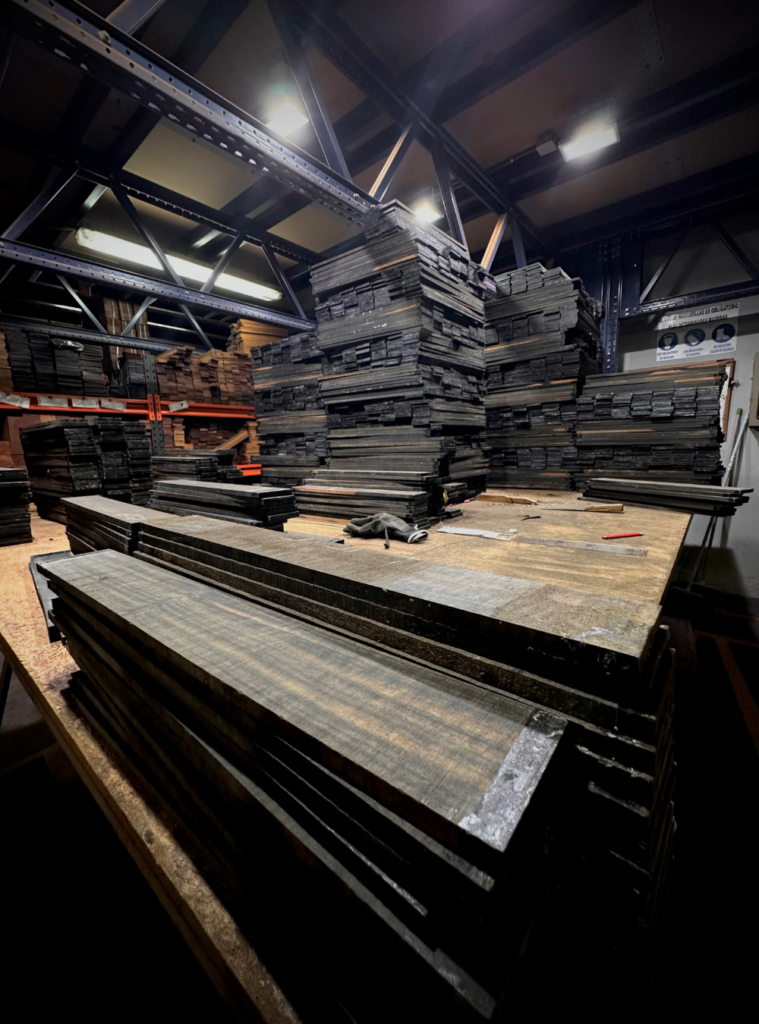
Ebony’s Introduction to the Lutherie Workshop
The use of ebony in lutherie dates back to the 16th century, when major European instrument-making workshops began experimenting with exotic woods brought by traders from Asia and Africa. Among these woods, ebony stood out for its uniform black color and exceptional hardness.
While early medieval string instruments primarily used local woods like maple and spruce, ebony was quickly adopted for components such as fingerboards, pegs, and tailpieces. Its resistance to wear and smooth texture made it the ideal material for parts of the instrument that are in constant contact with the musician’s hands.
Ebony in Modern Lutherie
Ebony is a wood that challenges both the luthier and the workshop tools. Its extreme density and compact texture allow for flawless finishes, making it ideal for fingerboards, pegs, and tailpieces. However, these same characteristics demand precision in craftsmanship—the cuts must be clean, and the polishing meticulous to highlight both its uniform surface and resistance to wear.
Ebony trees are not homogeneous; each trunk produces pieces with unique characteristics and varying qualities. At Maderas Barber, as producers, they offer ebony of different grades, reflecting a commitment to making the most of this valuable raw material. This taught me that the goal isn’t to seek perfect uniformity, but rather to understand the distinct qualities of each piece and how to use them effectively in the instrument. In the end, it is the luthier who defines the character of ebony through their craftsmanship.

Ebony: A Super Wood for Luthiers
Ebony is not just a wood; it is an essential element in the tradition of lutherie, a material that connects centuries of history with the hands of today’s luthiers. Each piece, with its nuances and challenges, presents an opportunity to create something unique.
For me, working with ebony is a constant lesson in humility and learning, a reminder that wood has as much character as the instrument it becomes a part of.
Did you know this story about ebony?
What other aspects of tonewoods in lutherie would you like to explore?
Leave your comment on the blog, and let’s keep the conversation going!